| 31. Dezember 2014
Die vierte industrielle Revolution
Neue Form der Automatisierungstechnologie mit dem Internet der Dinge
Eine ganz neue Form der industriellen Wertschöpfung – das ist die Idee von Industrie 4.0. Geräte, Automatisierung, Warenwirtschaft und Wartung werden zu cyber-physischen Systemen verknüpft. Echtzeitdaten steigern die Produktionsleistung und helfen, immer besser auf Kundenwünsche einzugehen. Mit den neuen Lösungen kommen neue Herausforderungen – beispielsweise für die Menschen in der Produktion und für die Sicherheit von wichtigen Daten.
In Zukunft werden Internettechnologien in Fabriken und Kraftwerken Einzug halten – mit dem Potenzial, die Automatisierung zu revolutionieren. Das zugehörige Schlagwort Industrie 4.0 wurde in Deutschland auch durch das Zukunftsprojekt der Bundesregierung geformt. Industrie 4.0 ist zugleich ein Synonym für die vierte industrielle Revolution. Als Schritte eins bis drei der Entwicklung gelten die frühe Industrialisierung mit dem Einsatz der Dampfmaschine, die Produktion mithilfe von Fliessbändern ab 1870 und die Steuerung von Anlagen und Prozessen durch speicherprogrammierbare Steuerung (SPS) seit den 1960er-Jahren.
Mit Industrie 4.0 eröffnet sich eine neue Welt von Innovationsmöglichkeiten. Die dynamische Vernetzung von Produkten, Geräten und Anlagen ermöglicht neue Formen der Flexibilität. Früher wurde alles handgefertigt, später kam die industrielle Massenproduktion, heute können zunehmend wieder individuelle Produkte gefertigt werden: zum Beispiel Fahrzeuge, deren Ausstattung exakt den Kundenwünschen entspricht. Diese Flexibilisierung der Produktion wird weiter zunehmen.
Ein wichtiger technischer Aspekt von Industrie 4.0 besteht darin, dass jedem physischen Objekt in einer Produktionsanlage ein Datenmodell im Netz zugeordnet wird. Internettechnologien vernetzen diese Datenobjekte miteinander. Die entstehenden Möglichkeiten sind kaum absehbar.
Chance für Europa
Obwohl Industrie 4.0 schon heute viele Diskussionen und Entwicklungsprozesse in Industrieunternehmen bestimmt, soll das Thema in Zukunft noch wichtiger werden. Die Roland-Berger-Studie «Industrie 4.0 – The new industrial revolution – How Europe will succeed» kommt beispielsweise zu dem Schluss, dass Europa hier an Bedeutung gewinnen kann und diese Chance nutzen sollte. Um der Industrie 4.0 zum Durchbruch zu verhelfen, seien in den kommenden 15 Jahren laut Roland Berger europaweit Investitionen in Höhe von 1350 Milliarden Euro notwendig.
In diesem Zusammenhang stellen die Marktforscher von Pierre Audoin Consultants fest, dass heute bereits 15 % der mittelständischen deutschen Fertiger Techniken der Industrie 4.0 einsetzen. Automotive-Unternehmen nehmen eine Vorreiterrolle ein: 80 % setzen bereits auf intelligente Produktionsanlagen, 9 % nutzen Selbststeuerung und Vernetzung.
Cyber-physisch tanken
Ein wesentliches Element in Szenarien von Industrie 4.0 sind cyber-physische Systeme – sie lassen sich am Beispiel von Tankstellen anschaulich erklären: Sämtliche Anlagen in Deutschland senden ihre Benzinpreise an eine zentrale Meldestelle. Dadurch existiert jede Tankstelle zwei Mal: als reales Objekt und als virtuelles Datenobjekt im Netz. Die Wertschöpfung findet darauf aufbauend statt – Apps ermitteln die preiswerteste Tankstelle in der Umgebung des Interessenten. Die drei Ebenen – physisches Objekt, Datenobjekt im Netz und App – bilden ein cyberphysisches System. «Neu an diesem Szenario sind nicht die Technologien, sondern deren Kombination auf neue Weise», sagt Rainer Drath, Program Manager und Senior Principal Scientist am ABB Forschungszentrum in Ladenburg (siehe Interview). «Die Tankstellenthematik – so einfach sie klingt – ist ein Musterbeispiel für die Idee und Denkweise hinter Industrie 4.0: Es beruht darauf, dass Tankstellenbetreiber herstellerübergreifend auf neue Weise vernetzt werden – mit standardisiertem Datenzugriff. Tankstellen-Apps werden bereits heute von Millionen von Menschen genutzt. Der Quantensprung ergibt sich aus der massenhaften Teilnahme der Tankstellen, der Verfügbarkeit von Echtzeitpreisinformationen und der Entwicklung sinnvoller Apps von Drittherstellern.»
Das Fraunhofer-Institut für Arbeitswirtschaft und Organisation IAO in Stuttgart hat in seiner Studie «Produktionsarbeit der Zukunft – Industrie 4.0» die neuen Technologien untersucht. «Wir wollten herausfinden, welche Herausforderungen sich mit Industrie 4.0 besser lösen lassen», sagt Tobias Krause, Diplom-Wirtschaftsinformatiker und wissenschaftlicher Mitarbeiter am IAO. «Zu den Herausforderungen zählt ein sich rasch verändernder Markt, der Produkte immer schneller und in vielen Varianten fordert.» Wenn die Industrie die technischen Möglichkeiten nutze, könne sie mit hochkomplexen Produkten und Produktvarianten erfolgreich sein. «Spannend im Szenario von Industrie 4.0 sind Verknüpfungen», sagt Tobias Krause. «Zur reinen Messung einer Öltemperatur kommt zum Beispiel die Analyse und Prognose, ob eine Maschine gewartet werden muss, um einem Ausfall vorzubeugen. Wir sehen anhand realer Echtzeitdaten, wie die Produktion im Moment steht, und entscheiden auf dieser Basis, wie wir weiter produzieren.»
«Industrie 4.0 darf in der Produktion kein Versuchsballon sein, sondern muss zuverlässig funktionieren.»
Schlüsselfaktor: menschliche Arbeit
Neben der technischen Ausgestaltung von Industrie 4.0 ist das künftige Zusammenspiel von Mensch und Automation ein entscheidender Aspekt der IAO-Studie. «Wir erwarten nicht, dass alles automatisiert wird. Eine vollautonome, menschenleere Produktion wird es nicht geben», sagt Tobias Krause. «Die menschliche Arbeit bleibt ein Schlüsselfaktor für Produktivität. Der Mensch kann intelligent reagieren, ohne für jede einzelne Situation programmiert zu sein; er ist kreativ, inhaltlich flexibel und stellt sich auf neue Arbeitsabläufe ein. Wenn die Mitarbeiter in der neuen Technik einen Mehrwert für die eigene Arbeit sehen, wird die Akzeptanz einfach zu erreichen sein.»
In der Produktion der Zukunft unterstützen mobile Kommunikationsmittel wie Mobiltelefone oder an der Montagestelle angebrachte Tabletcomputer die Mitarbeiter. «Das Ziel sollte sein, die Menschen als Entscheidungskompetenz mit ins System einzubeziehen. Dazu müssen sie die notwendigen Informationen passend aufbereitet erhalten», sagt Tobias Krause. «Mit den mobilen Kommunikationsmitteln ist es zusätzlich möglich, Kapazitätsflexibilität zu organisieren. Wenn eine Maschine defekt ist, können die vernetzten Mitarbeiter rasch abstimmen, wer die Reparatur beherrscht und verfügbar ist.»
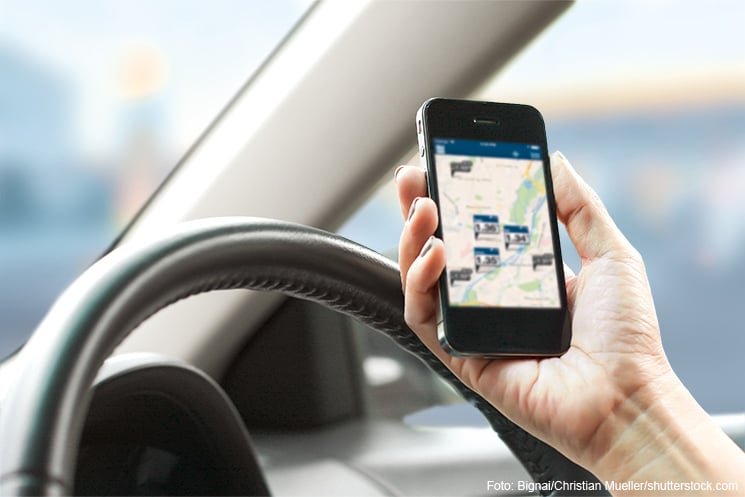
Machbares im Dienst des Sinnvollen
Bei der Entwicklung und Einführung entsprechender Systeme sind einige Herausforderungen zu meistern – von der grundlegenen Kosten-Nutzen-Rechnung ganz abgesehen. Jan Krückel, Leiter Produktmanagement und Applikationen Automation, Motors & Drives bei ABB Schweiz, nennt dazu die Fragen der Normierungen, der Sicherheit und der Stabilität. «Industrie 4.0 darf in der Produktion kein Versuchsballon sein, sondern muss zuverlässig funktionieren», betonte er in seinem Einführungsreferat am Ostschweizer Technologiesymposium Mitte August 2014 in St. Gallen, das dem Thema «Industrie 4.0» gewidmet war. Jedenfalls setze sich ABB dafür ein, das Machbare in den Dienst des Sinnvollen zu stellen.
Bevor dereinst die Produktionsarbeiter in der neu gearteten Fertigungsindustrie ans Werk gehen können, müssen zuerst einmal Anlagen konstruiert und elektrifiziert, die Software entworfen und die gemeinsame Funktion geprüft werden. «Wo bisher sequenziell zunächst Mechanik sowie Elektrik und danach die Software zum Test an der fertiggestellten Maschine bearbeitet wurden, werden das Engineering und die Inbetriebnahme parallelisiert», sagt Nicolas Mauser, Projektleiter in der Software-Entwicklung für den ABB Automation Builder. Hierbei kommen künftig Ansätze der Industrie 4.0 zum Tragen: «Für die Parallelisierung sind standardisierte Daten und ein virtuelles Modell notwendig, weil ein physisches Objekt schlichtweg noch nicht existiert.» Die am Computer konstruierten Anlagen können dann virtuell getestet und in Betrieb genommen werden. Man spricht vom Virtual Comissioning. Die Standardisierung von Planungsdaten und ein hoher Detailgrad bei virtuellen Inbetriebnahmen reduzieren signifikant die Inbetriebnahme- und Rüstzeiten sowie das Projektrisiko für Anlagenplaner und -betreiber.
Rüstzeiten minimieren
Das virtuelle Modell bietet zudem Vorteile für reale Anlagen. Beispielsweise können Produktionsparameter in das Modell zurückgespielt werden, um Hinweise zu Wartung und Anlagenoptimierung zu erhalten. Veränderungen an der Anlage, etwa bei Umrüstungen, können vorab im virtuellen Modell durchgeführt werden, was teure Stillstands- und Rüstzeiten minimiert. Generell rechnen sich die initialen Kosten des virtuellen Modells durch den Vorteil, schneller zu präziseren Kosten am Markt zu sein. Der Nutzen verstärkt sich durch die Verwendung über mehrere Maschinenzyklen hinweg. Ähnliches gilt für die Modularisierung in der Prozessindustrie.
«In der Automobilindustrie sind virtuelle Umrüstungen bereits üblich. Für den Maschinenbau eröffnen sich Chancen durch Standardisierungen und Bibliotheken. Wenn entsprechend definierte virtuelle Modelle zum Download bereitstehen, wird die gesamte Virtualisierung effizienter und wirtschaftlicher», sagt Nicolas Mauser. «Der ABB Automation Builder erfüllt bereits heute die technologischen Anforderungen an eine virtuelle Inbetriebnahme, aber die Prozesse zur Erstellung von Simulationsmodellen müssen noch deutlich effizienter gestaltet werden.»
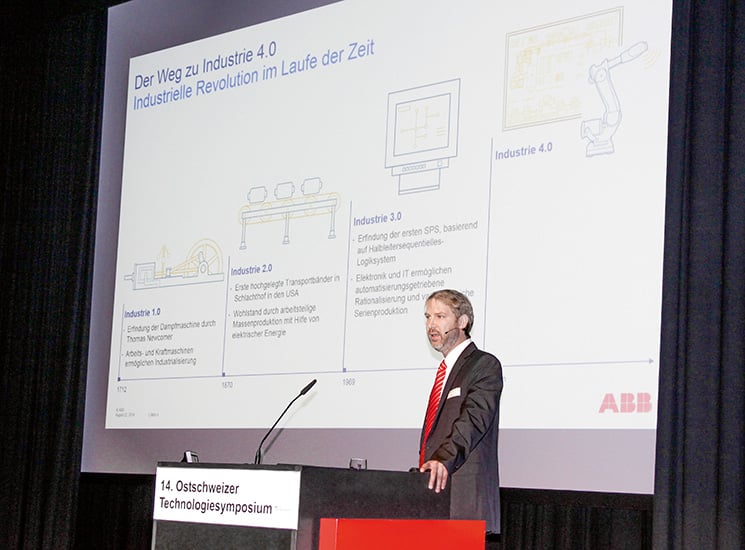
Standardisierte Daten notwendig
Um eine automatisierte Integration virtueller Geräte in ein gemeinsames Simulationsmodell zu ermöglichen, sollten elektrische und mechanische Daten, Steuerungs- sowie Simulationsdaten standardisiert vorliegen. Bei vielen, meist organisatorischen Hürden bietet Industrie 4.0 vielversprechende Ansätze: Geräte, die weitere Informationen mit sich führen, ethernet-basierte Kommunikation im gesamten Automatisierungssystem und einfache Integration durch die Standardisierung der Topologie, die ABB als Mitglied der Plattform Industrie 4.0 vorantreibt.
«Wir erwarten, dass Maschinenausrüster und Integratoren bei der virtuellen Inbetriebnahme den Vorreitern der Automobilindustrie folgen werden», sagt Nicolas Mauser. «Diesem Schritt werden dann auch mittelständische Komponenten-Hersteller folgen. Durch Industrie 4.0 wird sich der Prozess beschleunigen und die kritische Masse schneller erreicht.» Das würde bedeuten, dass Geräte und ihre Daten in standardisierten Formaten als virtuelle Modelle im Netz zur Verfügung stünden.
Angesichts von Industrie 4.0 sind Unternehmen jedoch auch mit neuen Herausforderungen in Bezug auf die Cyber Security konfrontiert. «Die immer stärkere Vernetzung vergrössert die Angriffsfläche. Es wird schwieriger, den Schutz der Netzwerkgrenze aufrechtzuerhalten. Bedrohungsmodelle, bei denen das eigene Netzwerk als potenziell gefährlich angesehen wird, gewinnen an Bedeutung», sagt Sebastian Obermeier, Senior Principal Scientist am Schweizer ABB-Konzernforschungszentrum in Baden-Dättwil. Der Spezialist für Cyber Security hat jedoch auch die Vorteile vor Augen: «Industrie 4.0 als zukünftiges Szenario gibt uns die Chance, Cyber Security als Basistechnologie direkt in die Entwicklung einfliessen zu lassen. Wir können von Grund auf ein System planen, das die identifizierten Bedrohungen so weit wie möglich abschwächt.»
Sicherheit als kontinuierlicher Prozess
Um Angriffen zu begegnen, sollte ein vielschichtiges Sicherheitskonzept etabliert werden, das ständig angepasst wird. «Sicherheit ist kein Produkt, das man einmal kauft, sondern ein kontinuierlicher Prozess», sagt Sebastian Obermeier. «Die einzelnen Lösungen sollten mit den in einer Bedrohungsanalyse erkannten Gefahren verknüpft werden. Falls Schutz – wie bei Geheimdienstangriffen – mit vertretbaren Mitteln nicht möglich ist, hat zumindest die Erkennung von Angriffen Priorität.»
Auch Produktionssysteme sollten im Kontext von Industrie 4.0 kontinuierlich angepasst werden. Für Leitsysteme bietet ABB das Automation Sentinel Life Cycle Management- und Supportprogramm an. Sicherheits-Updates von Microsoft sowie Patches, Scan-Engines und Updates der Virendefinitionsdateien werden dabei zunächst in einem Referenzlabor von ABB geprüft, bevor sie für den allgemeinen Einsatz freigegeben werden.
Der Cyber Security Monitoring Service von ABB identifiziert, klassifiziert und priorisiert Möglichkeiten zur Verbesserung der Sicherheit des Leitsystems. Der Nutzer greift auf den ABB Cyber Security Monitoring Service über den ABB ServicePort zu. Dabei handelt es sich um eine remotebasierte Plattform zur individuellen und sicheren Bereitstellung von Services sowie zur Einbindung von ABB-Experten.
«Wir erwarten, dass Maschinenausrüster und Integratoren bei der virtuellen Inbetriebnahme den Vorreitern der Automobilindustrie folgen werden.»
Härtung und Fuzzy Hashing
Um auch in Zukunft bestmöglichen Schutz bereitstellen zu können, forscht ABB an der Automatisierung von Sicherheitskonfigurationen, der digitalen Forensik, sicheren Architekturen und der Nachvollziehbarkeit von Benutzerinteraktionen. «Ein wichtiger Schritt bei der Konfiguration von Industrie-4.0-Anlagen ist eine sicherheitsrelevante Härtung, die alle Softwarebestandteile und Funktionen entfernt, die zur Erfüllung der eigentlichen Aufgabe des Systems nicht zwingend notwendig sind», sagt Sebastian Obermeier. «Zur Erkennung von Angriffen hat sich Fuzzy Hashing – ein Verfahren zur Ähnlichkeitsanalyse – als hilfreich herausgestellt. Mit dieser Methode können Veränderungen im Leitsystem anhand eines Ähnlichkeitswertes nachgewiesen und sehr gezielt analysiert werden.» Durch die vielfältige Zusammenarbeit mit der akademischen Forschung ist ABB auf zukünftige Anforderungen vorbereitet und kann die Aktivitäten im Bereich Cyber Security an die sich verändernde Landschaft anpassen und priorisieren.